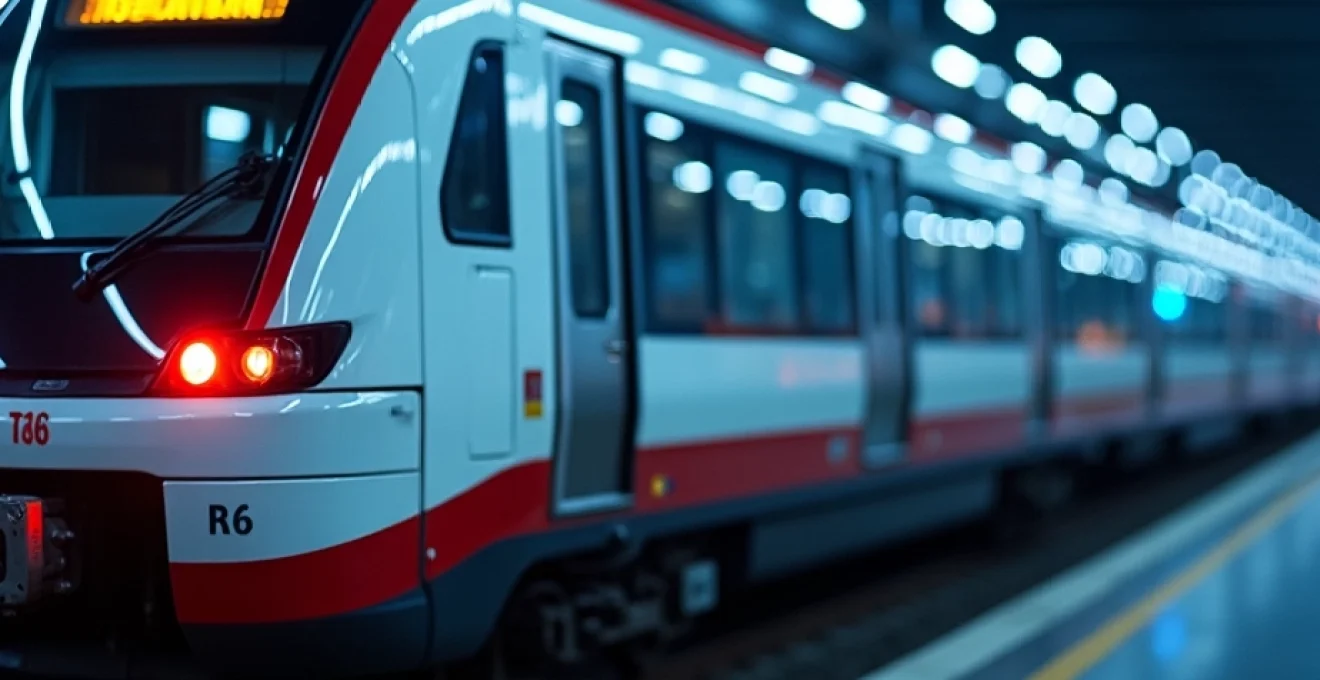
La production de pièces pour les trains modernes représente un défi technologique et logistique majeur dans l'industrie ferroviaire. Elle combine des processus de conception de pointe, des techniques de fabrication avancées et l'utilisation de matériaux innovants pour créer des composants à la fois performants, durables et respectueux de l'environnement. Cette évolution constante de la production ferroviaire vise à répondre aux exigences croissantes en matière de sécurité, de confort des passagers et d'efficacité énergétique, tout en s'adaptant aux contraintes économiques et écologiques actuelles.
Processus de conception des pièces ferroviaires modernes
La conception des pièces ferroviaires modernes débute par une phase d'ingénierie rigoureuse, utilisant des outils de conception assistée par ordinateur (CAO) de pointe. Ces logiciels permettent aux ingénieurs de créer des modèles 3D précis de chaque composant, en tenant compte des contraintes mécaniques, thermiques et aérodynamiques auxquelles ils seront soumis. La simulation numérique joue un rôle crucial dans cette étape, permettant de tester virtuellement les pièces dans diverses conditions avant même leur fabrication.
L'optimisation topologique est devenue un élément clé du processus de conception. Cette technique utilise des algorithmes complexes pour déterminer la distribution optimale du matériau au sein d'une pièce, réduisant son poids tout en conservant, voire en améliorant, ses propriétés mécaniques. Cette approche est particulièrement importante pour les composants structurels des trains, où chaque kilogramme économisé se traduit par une efficacité énergétique accrue.
La collaboration entre les équipes de conception, de production et de maintenance est essentielle tout au long du processus. Les retours d'expérience des opérateurs de maintenance sont intégrés dès les premières phases de conception, garantissant que les pièces sont non seulement performantes, mais aussi faciles à entretenir et à remplacer. Cette approche holistique de la conception contribue à réduire les coûts de cycle de vie des trains et à améliorer leur fiabilité opérationnelle.
Technologies de fabrication avancées pour composants de train
L'industrie ferroviaire adopte rapidement les technologies de fabrication avancées pour produire des pièces de train de haute qualité. Ces innovations permettent une production plus rapide, plus précise et souvent plus économique que les méthodes traditionnelles. Elles offrent également une plus grande flexibilité dans la conception et la personnalisation des composants.
Impression 3D métallique pour pièces complexes
L'impression 3D métallique, également connue sous le nom de fabrication additive, révolutionne la production de pièces ferroviaires complexes. Cette technologie permet de créer des composants avec des géométries intriquées qui seraient difficiles, voire impossibles, à réaliser avec les méthodes de fabrication conventionnelles. Les pièces imprimées en 3D peuvent être plus légères tout en conservant leur résistance structurelle, grâce à des structures internes optimisées.
Un exemple notable est la production de supports de freins pour les trains à grande vitesse. Ces pièces, traditionnellement fabriquées en plusieurs parties assemblées, peuvent désormais être imprimées en une seule pièce, réduisant ainsi le nombre de points de faiblesse potentiels et améliorant leur durabilité. La fabrication additive permet également de produire des pièces de rechange à la demande, réduisant les besoins en stockage et les délais d'approvisionnement.
Usinage CNC de précision pour bogies
L'usinage à commande numérique par ordinateur (CNC) joue un rôle crucial dans la fabrication de composants de train de haute précision, en particulier pour les bogies. Ces éléments essentiels, qui supportent le poids du train et assurent sa stabilité, nécessitent une précision extrême dans leur fabrication. Les machines CNC modernes peuvent usiner des pièces avec des tolérances de l'ordre du micron, garantissant un ajustement parfait et des performances optimales.
Les centres d'usinage 5 axes permettent de réaliser des opérations complexes en une seule installation, réduisant les temps de production et les risques d'erreur. La programmation avancée de ces machines, souvent assistée par l'intelligence artificielle, optimise les trajectoires d'outils pour une efficacité maximale et une qualité constante. L'usinage CNC est particulièrement adapté à la production de composants tels que les essieux, les roues et les pièces de suspension des bogies.
Moulage sous pression d'aluminium pour carrosseries légères
Le moulage sous pression d'aluminium est une technique de fabrication largement utilisée pour produire des composants de carrosserie de train légers et résistants. Ce processus implique l'injection d'aluminium fondu à haute pression dans un moule en acier, permettant de créer des pièces complexes avec une excellente finition de surface et une grande précision dimensionnelle.
Cette technique est particulièrement avantageuse pour la production de panneaux de carrosserie, de supports structurels et de composants intérieurs. Les alliages d'aluminium utilisés offrent un excellent rapport résistance/poids, contribuant à l'allègement global du train et à une meilleure efficacité énergétique. De plus, le moulage sous pression permet une cadence de production élevée, rendant cette méthode économiquement viable pour la production en série de pièces ferroviaires.
Soudage robotisé pour assemblages de châssis
Le soudage robotisé est devenu incontournable dans la fabrication des châssis de train modernes. Cette technologie offre une précision et une répétabilité inégalées, essentielles pour garantir l'intégrité structurelle des assemblages ferroviaires. Les robots de soudage équipés de systèmes de vision et de capteurs avancés peuvent adapter leurs paramètres en temps réel, assurant des soudures de haute qualité même sur des géométries complexes.
L'utilisation de robots pour le soudage permet également d'améliorer la sécurité des travailleurs en les éloignant des environnements dangereux. Les techniques de soudage innovantes, telles que le soudage par friction-malaxage ( friction stir welding ), sont de plus en plus intégrées aux processus robotisés, offrant des assemblages plus résistants et moins sujets aux déformations thermiques. Cette approche est particulièrement bénéfique pour l'assemblage de grandes structures comme les châssis de locomotive ou les caisses de wagon.
Matériaux innovants dans la production ferroviaire
L'évolution des matériaux utilisés dans la construction ferroviaire est un facteur clé de l'amélioration des performances et de la durabilité des trains modernes. Les ingénieurs et les chercheurs travaillent constamment à développer et à intégrer de nouveaux matériaux qui répondent aux exigences spécifiques de l'industrie ferroviaire, en termes de résistance, de légèreté et de durabilité.
Alliages d'aluminium à haute résistance pour structures
Les alliages d'aluminium à haute résistance sont de plus en plus utilisés dans la construction des structures de train. Ces matériaux offrent un excellent rapport résistance/poids, permettant de réduire significativement la masse des véhicules tout en maintenant leur robustesse. Les alliages de la série 7000, par exemple, sont particulièrement prisés pour leur résistance élevée et leur bonne résistance à la fatigue.
L'utilisation de ces alliages dans la fabrication des caisses de wagons et des structures de locomotive permet non seulement d'alléger les trains, mais aussi d'améliorer leur efficacité énergétique. De plus, la résistance naturelle de l'aluminium à la corrosion contribue à réduire les coûts de maintenance à long terme. Les techniques de soudage avancées, comme le soudage par friction-malaxage, sont souvent employées pour assembler ces alliages, garantissant des joints solides et durables.
Composites carbone-époxy pour réduction de poids
Les matériaux composites, en particulier les composites carbone-époxy, révolutionnent la conception des trains modernes. Ces matériaux offrent une résistance exceptionnelle pour un poids minimal, permettant des réductions de masse significatives par rapport aux matériaux traditionnels. Leur utilisation est particulièrement pertinente pour les panneaux de carrosserie, les éléments aérodynamiques et certaines pièces structurelles non critiques.
Les composites carbone-époxy présentent également d'excellentes propriétés d'amortissement des vibrations, contribuant à améliorer le confort des passagers. Leur résistance à la fatigue et à la corrosion les rend particulièrement adaptés aux environnements ferroviaires exigeants. Bien que leur coût initial soit plus élevé que celui des matériaux traditionnels, les économies réalisées sur le long terme en termes de consommation d'énergie et de maintenance justifient souvent cet investissement.
Aciers à très haute limite d'élasticité pour essieux
Les aciers à très haute limite d'élasticité (THLE) jouent un rôle crucial dans la fabrication des essieux de train, composants critiques pour la sécurité et les performances. Ces aciers spéciaux, souvent alliés au chrome, au molybdène et au nickel, offrent une résistance mécanique exceptionnelle tout en conservant une bonne ductilité. Cette combinaison de propriétés est essentielle pour supporter les charges dynamiques élevées auxquelles les essieux sont soumis.
L'utilisation d'aciers THLE permet de concevoir des essieux plus légers sans compromettre leur résistance, contribuant ainsi à réduire les masses non suspendues du train. Cela se traduit par une amélioration du comportement dynamique du véhicule et une réduction de l'usure des voies. Les techniques de traitement thermique avancées, telles que la trempe et le revenu contrôlés, sont essentielles pour optimiser les propriétés mécaniques de ces aciers.
Polymères techniques pour l'isolation phonique
Les polymères techniques jouent un rôle de plus en plus important dans l'amélioration du confort acoustique des trains modernes. Ces matériaux, qui incluent des polyuréthanes, des élastomères thermoplastiques et des composites à matrice polymère, sont utilisés pour créer des systèmes d'isolation phonique efficaces et légers. Leur capacité à absorber et à amortir les vibrations les rend particulièrement adaptés à la réduction du bruit dans les compartiments passagers.
L'utilisation de ces polymères s'étend également aux systèmes de suspension secondaire, où ils contribuent à isoler la caisse du train des vibrations provenant des bogies. Des formulations spécifiques de polymères sont développées pour résister aux conditions environnementales extrêmes rencontrées dans le secteur ferroviaire, y compris les variations de température et l'exposition aux UV. L'intégration de ces matériaux innovants permet non seulement d'améliorer le confort des passagers, mais aussi de réduire le poids global du train, contribuant ainsi à son efficacité énergétique.
Contrôle qualité et certifications des pièces de train
Le contrôle qualité est un aspect fondamental de la production de pièces pour les trains modernes. Chaque composant, du plus petit boulon au châssis principal, doit répondre à des normes strictes de sécurité et de performance. Les fabricants mettent en œuvre des processus de contrôle qualité rigoureux tout au long de la chaîne de production, utilisant des technologies avancées d'inspection et de test.
Les méthodes de contrôle non destructif (CND) sont largement utilisées dans l'industrie ferroviaire. Ces techniques, qui incluent les ultrasons, la radiographie et les courants de Foucault, permettent d'inspecter les pièces sans les endommager, détectant des défauts internes invisibles à l'œil nu. Pour les composants critiques comme les essieux et les roues, des tests de fatigue et de résistance sont systématiquement effectués pour simuler les conditions réelles d'utilisation sur de longues périodes.
La certification des pièces de train est un processus complexe qui implique souvent des organismes indépendants. Les normes internationales, telles que l'EN 15085 pour le soudage des véhicules et des composants ferroviaires, définissent des exigences strictes pour la production et le contrôle qualité. Les fabricants doivent obtenir et maintenir des certifications spécifiques pour pouvoir fournir des composants à l'industrie ferroviaire, garantissant ainsi un niveau élevé de sécurité et de fiabilité.
La qualité n'est pas un acte, c'est une habitude. Dans l'industrie ferroviaire, cette philosophie est inscrite dans chaque étape de la production, depuis la conception jusqu'à l'assemblage final.
L'utilisation croissante de l' Internet des Objets (IoT) et de l'analyse de données massives transforme également les approches de contrôle qualité. Des capteurs intégrés aux pièces peuvent désormais fournir des données en temps réel sur leur état et leurs performances, permettant une maintenance prédictive et une amélioration continue des processus de fabrication.
Chaîne logistique et approvisionnement des composants
La gestion de la chaîne logistique dans la production de pièces pour trains modernes est un défi complexe qui nécessite une coordination précise entre de nombreux acteurs. L'industrie ferroviaire dépend d'un réseau étendu de fournisseurs, allant des producteurs de matières premières aux fabricants de composants spécialisés. La gestion efficace de cette chaîne d'approvisionnement est cruciale pour maintenir des délais de production compétitifs et assurer la qualité des produits finis.
Les fabricants de trains adoptent de plus en plus des stratégies de lean manufacturing et de production juste-à-temps pour optimiser leurs processus. Ces approches visent à réduire les stocks et à minimiser les gaspillages, tout en maintenant une flexibilité suffisante pour répondre aux fluctuations de la demande. L'utilisation de systèmes de gestion de la chaîne logistique (SCM) avancés permet une visibilité en temps réel sur l'ensemble du processus d'approvisionnement, facilitant la prise de décision rapide en cas de perturbations.
La localisation des fournisseurs est un aspect important de la stratégie d'approvisionnement. De nombreux fabricants cherchent à réduire leur dépen
dance à l'égard des fournisseurs étrangers en développant des partenariats locaux. Cette approche permet non seulement de réduire les coûts et les délais de transport, mais aussi de stimuler l'économie locale et de répondre aux exigences de contenu local souvent imposées par les gouvernements. Cependant, pour certains composants spécialisés, le recours à des fournisseurs internationaux reste inévitable, nécessitant une gestion logistique internationale complexe.
La traçabilité des composants est un autre aspect crucial de la chaîne d'approvisionnement ferroviaire. Chaque pièce doit être suivie de sa fabrication à son installation, en passant par le transport et le stockage. Cette traçabilité est essentielle non seulement pour le contrôle qualité, mais aussi pour se conformer aux réglementations de sécurité et faciliter les rappels éventuels. Les technologies comme la RFID et les codes-barres 2D sont largement utilisées pour automatiser ce processus de suivi.
Développement durable dans la production ferroviaire
Le développement durable est devenu un impératif dans l'industrie ferroviaire, influençant profondément les pratiques de production des pièces de train. Les fabricants sont de plus en plus conscients de leur responsabilité environnementale et cherchent à minimiser l'impact écologique de leurs activités tout au long du cycle de vie des produits.
Recyclage et réutilisation des matériaux ferreux
Le recyclage des matériaux ferreux est une pratique bien établie dans l'industrie ferroviaire. L'acier, principal composant de nombreuses pièces de train, est hautement recyclable sans perte de qualité. Les fabricants mettent en place des systèmes de collecte et de tri des déchets métalliques générés pendant la production, ainsi que des programmes de récupération des pièces en fin de vie.
La réutilisation des matériaux va au-delà du simple recyclage. Certaines entreprises explorent des moyens innovants de donner une seconde vie aux composants usagés. Par exemple, les bogies en fin de vie peuvent être démontés, leurs pièces inspectées et, si elles sont en bon état, réutilisées dans la fabrication de nouveaux bogies ou d'autres composants. Cette approche d'économie circulaire permet non seulement de réduire la consommation de matières premières, mais aussi de diminuer l'énergie nécessaire à la production de nouvelles pièces.
Optimisation énergétique des processus de fabrication
L'optimisation énergétique est au cœur des efforts de durabilité dans la production ferroviaire. Les fabricants investissent dans des technologies et des pratiques visant à réduire la consommation d'énergie à chaque étape du processus de production. Cela inclut l'utilisation de machines-outils à haute efficacité énergétique, l'optimisation des processus thermiques comme le traitement thermique des aciers, et l'adoption de systèmes d'éclairage et de chauffage intelligents dans les usines.
L'intégration de sources d'énergie renouvelable dans les installations de production est une tendance croissante. De nombreux fabricants installent des panneaux solaires sur les toits de leurs usines ou investissent dans des parcs éoliens pour alimenter leurs opérations. Certains vont même jusqu'à développer des systèmes de récupération de l'énergie générée par les processus de production, comme la chaleur résiduelle des fours, pour la réutiliser dans d'autres parties de l'usine.
Conception éco-responsable avec l'analyse du cycle de vie
L'analyse du cycle de vie (ACV) est devenue un outil essentiel dans la conception éco-responsable des pièces de train. Cette méthode permet d'évaluer l'impact environnemental d'un produit tout au long de son existence, de l'extraction des matières premières à son élimination finale. Les ingénieurs utilisent les résultats de l'ACV pour identifier les points critiques où des améliorations peuvent être apportées pour réduire l'empreinte écologique du produit.
La conception éco-responsable va au-delà de la simple sélection de matériaux recyclables. Elle prend en compte des facteurs tels que la facilité de démontage pour la maintenance ou le recyclage, la durabilité des composants pour prolonger leur durée de vie, et l'optimisation des formes pour réduire le poids et la consommation d'énergie pendant l'utilisation. Cette approche holistique permet de créer des pièces de train qui sont non seulement performantes, mais aussi respectueuses de l'environnement tout au long de leur cycle de vie.
L'innovation durable dans la production ferroviaire n'est pas seulement une responsabilité environnementale, c'est aussi un avantage compétitif. Les entreprises qui excellent dans ce domaine sont mieux positionnées pour répondre aux exigences croissantes des clients et des régulateurs en matière de durabilité.
En adoptant ces pratiques de développement durable, l'industrie ferroviaire ne se contente pas de réduire son impact environnemental. Elle ouvre également la voie à des innovations qui peuvent améliorer les performances, réduire les coûts d'exploitation à long terme et renforcer l'attrait du transport ferroviaire comme mode de déplacement écologique. La production de pièces pour les trains modernes devient ainsi un exemple de la façon dont l'industrie peut concilier progrès technologique et responsabilité environnementale.