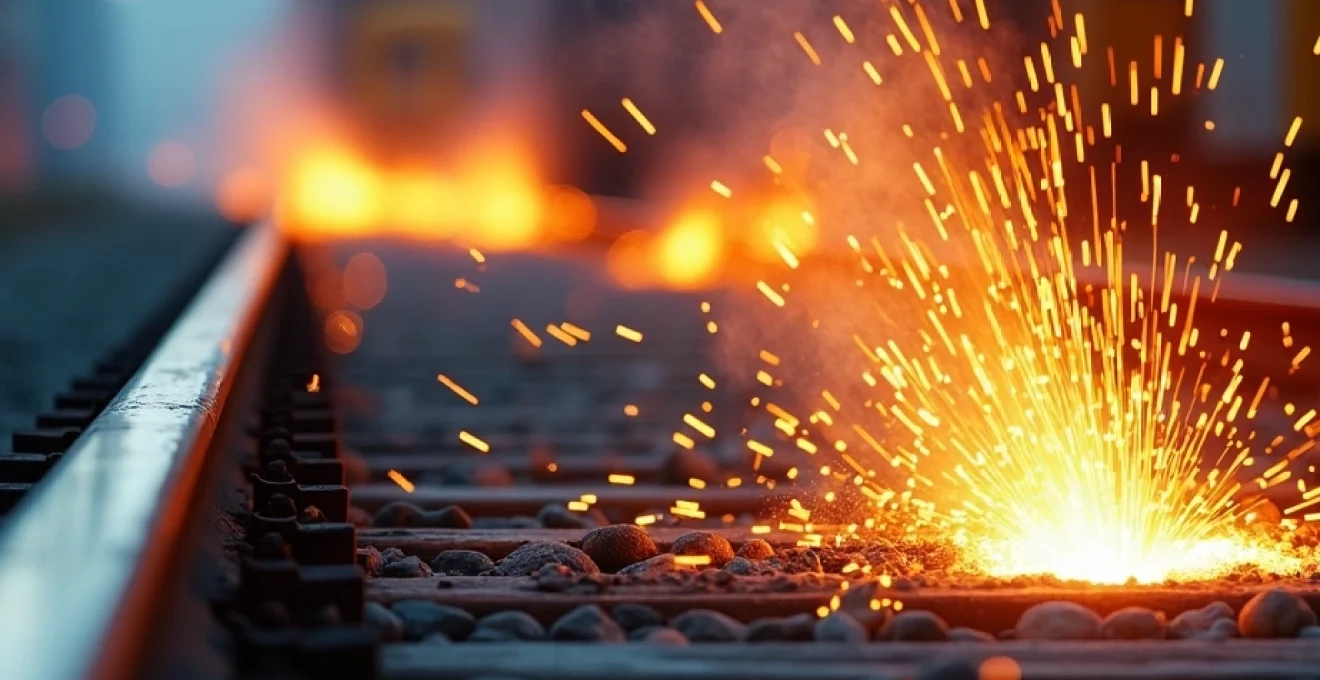
L'infrastructure ferroviaire, pierre angulaire du transport moderne, a connu une évolution remarquable depuis ses débuts au XIXe siècle. Au cœur de cette transformation se trouve le rail, élément crucial dont la fabrication a considérablement évolué au fil des décennies. Les techniques de production des rails d'aujourd'hui sont le fruit d'innovations constantes, répondant aux exigences croissantes en termes de sécurité, de performance et de durabilité. Cette révolution silencieuse dans la métallurgie ferroviaire a permis l'avènement de réseaux ferrés plus rapides, plus sûrs et plus économiques. Explorons ensemble comment la fabrication des rails s'est métamorphosée, passant d'un processus artisanal à une industrie de haute technologie.
Évolution des techniques de fabrication des rails depuis le XIXe siècle
Au début de l'ère ferroviaire, la production de rails était un processus laborieux et relativement rudimentaire. Les premiers rails étaient fabriqués en fonte, un matériau fragile et peu adapté aux contraintes du transport ferroviaire. La révolution industrielle a marqué un tournant décisif avec l'introduction de l'acier dans la fabrication des rails. Cette innovation a considérablement amélioré leur résistance et leur longévité.
Le procédé Bessemer, inventé au milieu du XIXe siècle, a permis la production d'acier à grande échelle, révolutionnant ainsi l'industrie ferroviaire. Les rails en acier Bessemer étaient plus solides et plus durables que leurs prédécesseurs en fonte. Cependant, ce procédé présentait des limitations en termes de contrôle de la qualité et de la composition de l'acier.
L'avènement du procédé Martin-Siemens à la fin du XIXe siècle a marqué une nouvelle étape dans l'amélioration de la qualité des rails. Cette technique permettait un meilleur contrôle de la composition chimique de l'acier, résultant en des rails plus homogènes et résistants. Les ingénieurs de l'époque ont progressivement affiné les alliages et les profils des rails pour répondre aux besoins spécifiques des différents types de voies ferrées.
Au début du XXe siècle, l'introduction du laminage à chaud a permis d'obtenir des rails de forme plus précise et de longueur accrue. Cette technique, qui consiste à faire passer l'acier chaud entre des rouleaux pour lui donner sa forme finale, est toujours utilisée aujourd'hui, bien qu'elle ait été considérablement améliorée et automatisée.
Procédés métallurgiques modernes dans la production ferroviaire
Les techniques de fabrication des rails ont connu une véritable révolution au cours des dernières décennies. L'industrie ferroviaire a adopté des procédés métallurgiques de pointe pour produire des rails de qualité supérieure, capables de résister aux contraintes extrêmes imposées par les trains modernes, notamment ceux à grande vitesse.
Coulée continue et laminage à chaud des rails en acier
La coulée continue est devenue la norme dans la production moderne de rails. Ce procédé permet de transformer l'acier liquide directement en barres semi-finies, éliminant ainsi plusieurs étapes intermédiaires du processus traditionnel. Cette technique améliore non seulement l'efficacité de la production, mais aussi la qualité et l'homogénéité du métal.
Le laminage à chaud, quant à lui, a été perfectionné pour atteindre des niveaux de précision inégalés. Les laminoirs modernes sont équipés de systèmes de contrôle informatisés qui ajustent en temps réel la pression et la température pour obtenir des rails aux dimensions exactes. Cette précision est cruciale pour assurer la sécurité et le confort des passagers, ainsi que pour réduire l'usure des roues des trains.
Traitement thermique pour l'amélioration de la résistance à l'usure
L'un des développements les plus significatifs dans la fabrication des rails est l'introduction de traitements thermiques avancés. Ces procédés permettent d'améliorer considérablement les propriétés mécaniques de l'acier, notamment sa dureté et sa résistance à l'usure. Le traitement thermique le plus couramment utilisé est la trempe et le revenu, qui consiste à chauffer le rail à haute température puis à le refroidir rapidement avant de le réchauffer à une température plus basse.
Cette technique crée une structure cristalline optimale dans l'acier, augmentant ainsi la durée de vie des rails et réduisant les besoins en maintenance. Certains fabricants ont développé des procédés propriétaires, comme le HH
(Head Hardened) ou le HSH
(Heat-Treated, Super-Hard), qui produisent des rails particulièrement résistants pour les lignes à fort trafic ou à grande vitesse.
Contrôle qualité par ultrasons et radiographie industrielle
La qualité des rails modernes est assurée par des méthodes de contrôle non destructives sophistiquées. Les ultrasons sont utilisés pour détecter les défauts internes invisibles à l'œil nu, tandis que la radiographie industrielle permet d'obtenir des images détaillées de la structure interne des rails. Ces techniques permettent d'identifier et d'éliminer les rails défectueux avant leur installation, garantissant ainsi un niveau de sécurité sans précédent.
Les systèmes de contrôle qualité sont souvent intégrés directement dans les lignes de production, permettant une vérification en temps réel et une traçabilité complète de chaque rail produit. Cette approche proactive de la qualité a considérablement réduit les risques de défaillance en service et a contribué à l'amélioration globale de la fiabilité des réseaux ferroviaires.
Alliages innovants pour rails à haute performance
La recherche métallurgique ne cesse de progresser, donnant naissance à de nouveaux alliages conçus spécifiquement pour les applications ferroviaires. Ces alliages innovants combinent une résistance accrue à l'usure avec une meilleure résistance à la fatigue et à la corrosion. Par exemple, certains fabricants ont développé des aciers au bore ou au vanadium qui offrent des performances supérieures dans des conditions extrêmes.
Les rails en acier bainitique représentent une avancée particulièrement prometteuse. Cette microstructure particulière de l'acier offre un excellent équilibre entre dureté et ténacité, ce qui se traduit par une durée de vie prolongée et une réduction des coûts de maintenance. Ces développements illustrent comment la métallurgie moderne continue de repousser les limites de ce qui est possible dans la conception des rails.
Automatisation et robotisation dans les usines de rails
L'industrie ferroviaire a embrassé la quatrième révolution industrielle, intégrant massivement l'automatisation et la robotisation dans ses processus de fabrication. Cette évolution a non seulement amélioré la productivité et la qualité, mais a également permis d'atteindre des niveaux de précision et de constance impossibles avec les méthodes manuelles traditionnelles.
Systèmes de production intégrés de voestalpine
Voestalpine, l'un des leaders mondiaux dans la production de rails, a mis en place des systèmes de production entièrement intégrés et automatisés. Ces installations de pointe utilisent des robots pour manipuler les rails tout au long du processus de fabrication, depuis la coulée de l'acier jusqu'à l'emballage final. Les systèmes de contrôle informatisés assurent une surveillance constante de tous les paramètres de production, permettant des ajustements en temps réel pour maintenir une qualité optimale.
L'un des aspects les plus impressionnants de ces systèmes est leur capacité à s'adapter rapidement à différents types de rails. En quelques minutes, une ligne de production peut passer de la fabrication de rails standards à celle de rails spéciaux pour les lignes à grande vitesse, avec un minimum d'intervention humaine.
Technologies de soudage automatisé des longs rails
Le soudage des rails est une étape critique dans la production de voies ferrées modernes. Les technologies de soudage automatisé ont révolutionné ce processus, permettant la création de longs rails soudés (LRS) avec une précision et une fiabilité inégalées. Ces systèmes utilisent des techniques avancées comme le soudage par étincelage ou le soudage aluminothermique contrôlé par ordinateur.
Les robots de soudage sont capables de réaliser des soudures parfaites en quelques minutes, sans variation de qualité due à la fatigue ou à l'erreur humaine. Cette uniformité est cruciale pour la sécurité et le confort des passagers, car elle élimine les irrégularités qui pourraient causer des vibrations ou des chocs lors du passage des trains.
Inspection par vision artificielle et apprentissage automatique
L'inspection des rails, autrefois une tâche manuelle laborieuse, est désormais réalisée par des systèmes de vision artificielle couplés à des algorithmes d'apprentissage automatique. Ces technologies permettent une inspection à 100% de chaque rail produit, à des vitesses bien supérieures à ce qui serait possible manuellement.
Les caméras haute résolution capturent des images détaillées de la surface et du profil des rails, tandis que les logiciels d'analyse d'images détectent instantanément la moindre imperfection. L'apprentissage automatique permet à ces systèmes de s'améliorer continuellement, devenant de plus en plus précis dans la détection des défauts subtils qui pourraient échapper à l'œil humain.
Innovations dans la conception géométrique des rails
La géométrie des rails a considérablement évolué depuis les premiers jours du chemin de fer. Les ingénieurs modernes utilisent des outils de conception assistée par ordinateur (CAO) et des simulations numériques avancées pour optimiser la forme des rails. Ces innovations visent à améliorer la stabilité des trains, réduire l'usure et minimiser le bruit et les vibrations.
Un exemple notable est le développement de profils de rail asymétriques pour les courbes. Ces rails spécialement conçus répartissent mieux les forces de contact entre la roue et le rail, réduisant ainsi l'usure et améliorant la sécurité dans les virages serrés. De même, les rails à gorge utilisés dans les tramways urbains ont été optimisés pour s'intégrer harmonieusement dans l'environnement urbain tout en offrant des performances supérieures.
Les recherches actuelles se concentrent sur des concepts encore plus avancés, comme les rails à profil variable qui s'adaptent aux différentes sections d'une ligne ferroviaire. Ces innovations pourraient révolutionner la conception des voies ferrées, offrant une flexibilité sans précédent dans l'optimisation des performances sur l'ensemble du réseau.
Techniques de pose et d'assemblage des voies ferrées modernes
La fabrication des rails n'est qu'une partie de l'équation. Les techniques de pose et d'assemblage des voies ferrées ont également connu des avancées significatives, contribuant à l'amélioration globale des infrastructures ferroviaires.
Pose de voie sur dalle béton pour lignes à grande vitesse
Les lignes à grande vitesse modernes utilisent souvent des systèmes de voie sur dalle en béton plutôt que le traditionnel ballast. Cette technique offre une stabilité supérieure et nécessite moins d'entretien, ce qui est crucial pour les trains circulant à des vitesses élevées. La pose de ces voies fait appel à des équipements hautement spécialisés qui assurent un alignement parfait des rails sur de longues distances.
Les dalles en béton sont préfabriquées avec une précision millimétrique et installées à l'aide de grues et de systèmes de positionnement GPS. Cette méthode permet une installation rapide et précise, réduisant considérablement le temps de construction des nouvelles lignes.
Soudage aluminothermique des rails in situ
Le soudage aluminothermique reste la méthode privilégiée pour assembler les rails sur le terrain. Cette technique, qui utilise la réaction exothermique entre l'aluminium et l'oxyde de fer pour créer une soudure solide, a été considérablement améliorée au fil des ans. Les kits de soudage modernes sont plus sûrs, plus faciles à utiliser et produisent des soudures de qualité supérieure.
Les équipes de pose utilisent désormais des équipements automatisés pour préparer les extrémités des rails et contrôler précisément le processus de soudage. Des systèmes de contrôle non destructif portatifs sont utilisés immédiatement après le soudage pour vérifier la qualité de chaque joint, assurant ainsi l'intégrité de la voie.
Systèmes de fixation élastique pandrol et vossloh
Les systèmes de fixation des rails ont également évolué pour répondre aux exigences des trains modernes. Les attaches élastiques, comme celles produites par Pandrol et Vossloh, sont devenues la norme dans de nombreux pays. Ces systèmes offrent une flexibilité contrôlée qui absorbe les vibrations et les chocs, tout en maintenant fermement le rail en place.
Ces fixations sont conçues pour être facilement installées et remplacées, réduisant ainsi les temps de maintenance. Certains modèles intègrent même des capteurs qui permettent une surveillance en temps réel de l'état de la voie, contribuant à une maintenance prédictive plus efficace.
Défis futurs et recherches en cours sur les rails ferroviaires
Malgré les progrès considérables réalisés dans la fabrication et l'installation des rails, l'industrie ferroviaire continue de faire face à de nombreux défis. Les chercheurs et les ingénieurs travaillent sur plusieurs fronts pour développer la prochaine génération de technologies ferroviaires.
L'un des domaines de recherche les plus prometteurs concerne les matériaux composites. Des expériences sont menées sur des rails en fibre de carbone ou en matériaux hybrides métal-composite, qui pourraient offrir un rapport résistance/poids encore plus avantageux que l'acier traditionnel. Ces matériaux pourraient permettre la construction de voies plus légères et plus faciles à installer, tout en conservant ou même en améliorant les performances des rails actuels.
La durabilité environnementale est également au cœur des préoccupations.
Les recherches se concentrent sur le développement de rails plus écologiques, tant dans leur production que dans leur utilisation. Des techniques de recyclage avancées sont explorées pour réduire l'empreinte carbone de la production de rails, tandis que des revêtements innovants sont étudiés pour réduire la friction et donc la consommation d'énergie des trains.
L'intégration de capteurs directement dans les rails est un autre domaine d'innovation prometteur. Ces "rails intelligents" pourraient fournir des données en temps réel sur leur état, la température, les vibrations et même le passage des trains. Cette technologie pourrait révolutionner la maintenance prédictive et améliorer considérablement la sécurité et l'efficacité des réseaux ferroviaires.
Enfin, la recherche s'intéresse également à l'adaptation des infrastructures ferroviaires aux conditions climatiques extrêmes, en anticipation des effets du changement climatique. Des rails capables de mieux résister aux variations de température extrêmes ou aux inondations sont en cours de développement, visant à rendre les réseaux ferroviaires plus résilients face aux défis environnementaux futurs.
En conclusion, bien que les principes fondamentaux de la fabrication des rails n'aient pas radicalement changé depuis le XIXe siècle, les techniques et les technologies utilisées ont connu une évolution spectaculaire. De la métallurgie de pointe à l'automatisation robotisée, en passant par les innovations dans la conception et l'installation, chaque aspect de la production et de l'utilisation des rails a été optimisé et amélioré. Ces avancées ont permis la création de réseaux ferroviaires plus rapides, plus sûrs et plus efficaces que jamais.
Alors que nous regardons vers l'avenir, il est clair que l'innovation dans le domaine des rails ferroviaires ne montre aucun signe de ralentissement. Les défis posés par la nécessité de transports plus durables et efficaces continueront de stimuler la recherche et le développement dans ce domaine crucial de l'infrastructure. Les rails du futur seront probablement plus intelligents, plus écologiques et plus adaptables que jamais, ouvrant la voie à une nouvelle ère du transport ferroviaire.