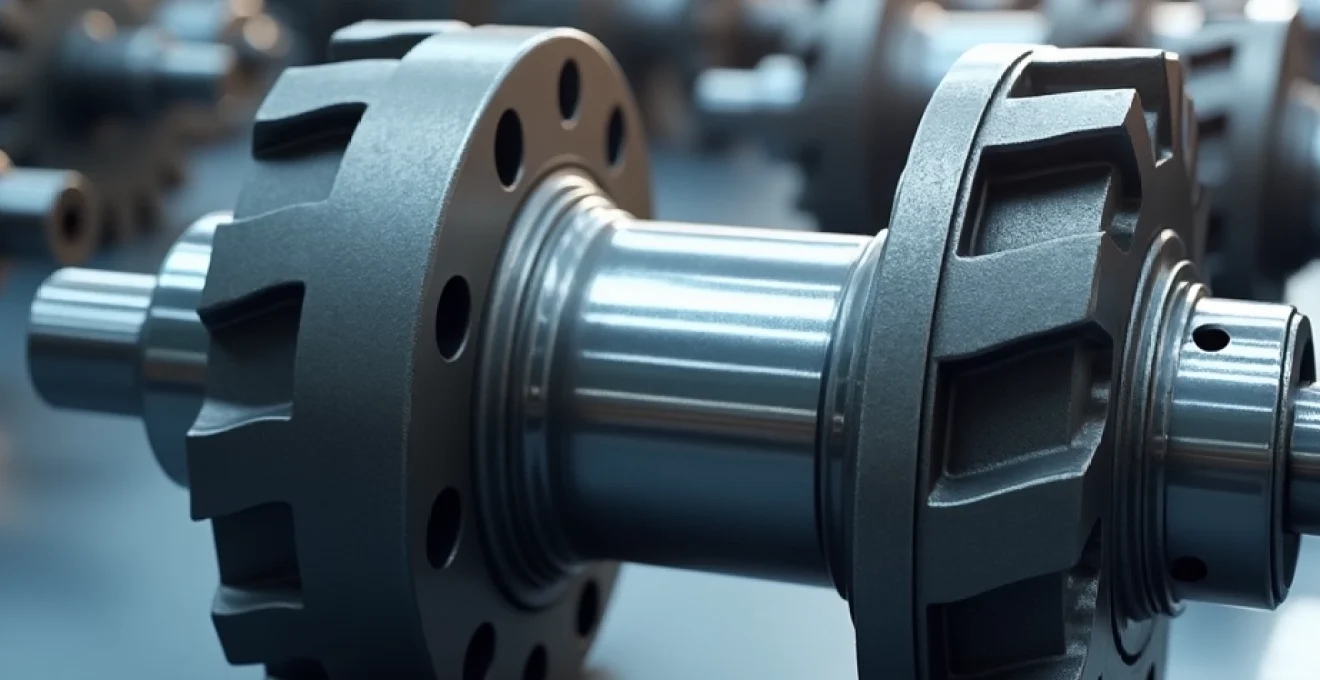
La fabrication des essieux de trains représente un défi technologique majeur dans l'industrie ferroviaire. Ces composants critiques, soumis à des contraintes extrêmes, jouent un rôle crucial dans la sécurité et les performances des véhicules sur rails. De la métallurgie à la conception en passant par l'usinage et les contrôles qualité, chaque étape de leur production requiert une expertise pointue et une rigueur sans faille. Les exigences toujours plus élevées en termes de fiabilité, de durée de vie et d'allègement des structures poussent les fabricants à repousser constamment les limites de l'innovation. Plongeons au cœur des défis complexes que doivent relever les ingénieurs et techniciens pour produire ces pièces essentielles du matériel roulant ferroviaire.
Contraintes métallurgiques dans la fabrication des essieux
Composition et traitement thermique des aciers pour essieux
La métallurgie des essieux de trains est un domaine exigeant qui nécessite une maîtrise parfaite de la composition et du traitement thermique des aciers. Les nuances utilisées doivent allier résistance mécanique élevée et ténacité pour supporter les sollicitations cycliques extrêmes. La teneur en carbone, généralement comprise entre 0,40% et 0,50%, ainsi que les éléments d'alliage comme le manganèse, le chrome ou le molybdène sont finement ajustés pour obtenir les propriétés recherchées.
Le traitement thermique joue un rôle clé dans l'obtention de la microstructure optimale. La trempe et le revenu permettent d'atteindre un compromis entre dureté et ductilité. La maîtrise des paramètres comme les vitesses de chauffe et de refroidissement est cruciale pour éviter la formation de zones fragiles. Les gradients thermiques dans la masse de l'essieu constituent un véritable défi, en particulier pour les grandes sections.
Contrôle des inclusions non métalliques et de la ségrégation
La propreté inclusionnaire des aciers pour essieux est primordiale pour garantir leur tenue en fatigue. Les inclusions non métalliques, en particulier les oxydes et les sulfures, agissent comme des amorces de fissures sous l'effet des sollicitations cycliques. Les techniques d'élaboration comme la métallurgie sous vide ou le traitement au calcium permettent de réduire drastiquement la teneur en inclusions néfastes.
La ségrégation des éléments d'alliage, en particulier le carbone et le soufre, peut créer des hétérogénéités de structure préjudiciables. Le contrôle de la solidification des lingots et l'optimisation des procédés de forgeage visent à limiter ces phénomènes. Des techniques avancées comme l'analyse par spectrométrie de masse à décharge luminescente permettent de caractériser finement les gradients de composition.
Techniques de forgeage et mise en forme des essieux
Le forgeage des essieux est une étape critique qui conditionne leurs propriétés mécaniques finales. Les opérations successives de refoulage, d'étirage et de finition doivent être parfaitement maîtrisées pour obtenir la structure métallurgique souhaitée. Le contrôle des taux de corroyage, c'est-à-dire du degré de déformation à chaud du métal, est essentiel pour affiner la structure et refermer la porosité centrale des lingots.
Les techniques de forgeage radial permettent d'optimiser l'écoulement du métal et d'obtenir des fibres orientées de manière favorable vis-à-vis des contraintes en service. La maîtrise des températures tout au long du processus est cruciale pour éviter la formation de défauts comme les replis ou les criques. Les simulations numériques par éléments finis sont aujourd'hui largement utilisées pour optimiser les gammes de forgeage.
Défis liés aux processus d'usinage de précision
Tolérances dimensionnelles critiques pour les portées de roulement
L'usinage des essieux de trains requiert une précision extrême, en particulier pour les portées de roulement. Les tolérances dimensionnelles et géométriques sont de l'ordre du micromètre pour garantir un montage optimal des roulements. La maîtrise des déformations liées aux contraintes résiduelles lors de l'enlèvement de matière constitue un véritable défi.
Les techniques d'usinage par tournage dur ou rectification de haute précision sont mises en œuvre pour atteindre les états de surface requis, avec des rugosités de l'ordre de 0,4 μm Ra. Le contrôle en continu des cotes et des géométries par des systèmes de mesure laser ou par contact est indispensable pour garantir la conformité des pièces.
Gestion de l'intégrité de surface et des contraintes résiduelles
L'intégrité de surface des essieux est un paramètre critique pour leur tenue en fatigue. Les opérations d'usinage peuvent générer des contraintes résiduelles néfastes en surface, favorisant l'amorçage de fissures. Des techniques comme le galetage ou le grenaillage de précontrainte permettent d'introduire des contraintes de compression bénéfiques en surface.
La maîtrise de l'échauffement lors de l'usinage est essentielle pour éviter les transformations métallurgiques superficielles. L'utilisation de lubrifiants haute performance et l'optimisation des conditions de coupe (vitesse, avance, profondeur de passe) permettent de limiter les échauffements locaux. Des contrôles métallographiques et des mesures de micro-dureté sont réalisés pour vérifier l'absence d'altération de la structure en surface.
Techniques d'usinage avancées pour les aciers à haute résistance
L'usinage des aciers à haute résistance utilisés pour les essieux modernes pose des défis spécifiques. Leur usinabilité réduite nécessite l'emploi d'outils de coupe performants, comme les plaquettes en céramique ou en carbure revêtu. Les techniques d'usinage assisté par ultrasons ou par jet d'eau haute pression permettent d'améliorer la productivité et la qualité des usinages.
L'usinage à sec ou avec lubrification minimale (MQL) se développe pour réduire l'impact environnemental. Ces techniques nécessitent cependant une maîtrise accrue des paramètres de coupe et de l'évacuation des copeaux. L'utilisation de la surveillance d'usinage en temps réel, basée sur l'analyse des efforts de coupe ou des vibrations, permet d'optimiser les processus et de détecter précocement les dérives.
Enjeux des contrôles non destructifs des essieux
Méthodes ultrasonores pour la détection des défauts internes
Le contrôle ultrasonore est la méthode de référence pour la détection des défauts internes dans les essieux. Les techniques multiéléments permettent une inspection rapide et fiable de l'ensemble du volume. La sensibilité de détection, de l'ordre du millimètre, nécessite une parfaite maîtrise des paramètres d'inspection et de la caractérisation des indications.
L'interprétation des signaux ultrasonores reste un défi majeur, en particulier pour discriminer les défauts réels des artéfacts liés à la structure métallurgique. L'utilisation de l'intelligence artificielle et des techniques de machine learning ouvre de nouvelles perspectives pour améliorer la fiabilité des diagnostics. La qualification des opérateurs et la validation des procédures selon les normes en vigueur sont cruciales pour garantir la qualité des contrôles.
Contrôles magnétoscopiques pour les fissures de surface
La magnétoscopie est largement utilisée pour la détection des fissures débouchantes sur les essieux. Cette méthode sensible permet de révéler des défauts de quelques dixièmes de millimètre. La maîtrise des paramètres comme l'intensité du champ magnétique ou la qualité des produits indicateurs est essentielle pour garantir la fiabilité des contrôles.
L'automatisation des contrôles magnétoscopiques, avec l'utilisation de bancs robotisés et de systèmes de vision, permet d'améliorer la reproductibilité et la traçabilité des inspections. La gestion des indications non pertinentes, comme les rayures d'usinage, reste un défi pour optimiser la productivité des contrôles. Des techniques avancées comme la magnétoscopie multi-fréquences offrent de nouvelles possibilités pour améliorer la discrimination des défauts.
Systèmes automatisés de contrôle en ligne de production
L'intégration des contrôles non destructifs directement dans les lignes de production est un enjeu majeur pour améliorer la qualité et réduire les coûts. Les systèmes automatisés combinent généralement plusieurs techniques comme les ultrasons, les courants de Foucault et la vision optique pour une inspection exhaustive des essieux.
La gestion des grands volumes de données générées par ces systèmes pose de nouveaux défis en termes de stockage, d'analyse et de traçabilité. L'utilisation du cloud computing et des techniques de big data permet d'optimiser le traitement des informations. La cybersécurité des systèmes de contrôle devient également un enjeu critique pour garantir l'intégrité des résultats.
Challenges de la conception pour la fatigue et la durabilité
Modélisation par éléments finis des contraintes dynamiques
La conception des essieux modernes s'appuie largement sur la modélisation numérique par éléments finis. Ces simulations permettent d'analyser finement la distribution des contraintes sous les sollicitations complexes rencontrées en service. La prise en compte des effets dynamiques, comme les chocs au passage des appareils de voie, constitue un véritable défi de modélisation.
L'intégration des données issues du monitoring en service permet d'affiner les modèles et de mieux prendre en compte les conditions réelles d'exploitation. Les techniques de jumeau numérique ouvrent de nouvelles perspectives pour le suivi en temps réel de l'état de fatigue des essieux. La validation des modèles par des essais en vraie grandeur reste cependant indispensable pour garantir leur fiabilité.
Optimisation topologique pour la réduction de masse
L'allègement des essieux est un enjeu majeur pour réduire la consommation énergétique et l'impact sur l'infrastructure. Les techniques d'optimisation topologique permettent de concevoir des géométries innovantes, maximisant la résistance pour une masse donnée. La prise en compte des contraintes de fabrication, comme les rayons de raccordement minimaux pour le forgeage, complexifie cependant le processus d'optimisation.
L'utilisation de matériaux avancés comme les aciers bainitiques ou les alliages d'aluminium à haute résistance ouvre de nouvelles possibilités pour l'allègement. L'hybridation des matériaux, avec par exemple l'utilisation de fibres de carbone pour le renforcement local, est également explorée. La validation de ces concepts innovants nécessite cependant des campagnes d'essais approfondies pour garantir leur fiabilité à long terme.
Tests de fatigue accélérés et validation des prototypes
La validation expérimentale des nouveaux concepts d'essieux reste une étape incontournable. Les essais de fatigue accélérés, réalisés sur des bancs spécialisés, permettent de simuler plusieurs années d'exploitation en quelques mois. La représentativité de ces essais vis-à-vis des conditions réelles d'utilisation constitue cependant un défi majeur.
L'instrumentation avancée des essieux en test, avec l'utilisation de jauges de déformation à fibres optiques ou de techniques d'émission acoustique, permet un suivi précis de l'évolution des dommages. Les méthodes statistiques comme les plans d'expériences ou l'analyse de fiabilité sont largement utilisées pour optimiser les campagnes d'essais et extrapoler les résultats à l'ensemble de la population d'essieux.
Normes et certifications spécifiques aux essieux ferroviaires
Exigences de la norme EN 13261 pour les essieux montés
La norme européenne EN 13261 définit les exigences techniques pour les essieux montés des véhicules ferroviaires. Elle couvre l'ensemble du cycle de vie, de la conception à la maintenance en passant par la fabrication et les contrôles. Les spécifications concernant les propriétés mécaniques, la géométrie ou encore la propreté inclusionnaire des aciers sont particulièrement strictes.
La conformité à cette norme nécessite la mise en place de processus de contrôle rigoureux tout au long de la chaîne de production. La traçabilité complète des opérations, depuis l'élaboration de l'acier jusqu'aux contrôles finaux, est un point clé. Les fabricants doivent démontrer leur capacité à maintenir un niveau de qualité constant sur le long terme pour obtenir la certification.
Processus de qualification des fournisseurs selon l'ISO/TS 22163
La norme ISO/TS 22163, spécifique au secteur ferroviaire, définit les exigences pour les systèmes de management de la qualité des fournisseurs. Elle impose une approche basée sur les risques et l'amélioration continue des processus. Pour les fabricants d'essieux, cela se traduit par la mise en place de contrôles renforcés et d'une traçabilité accrue à toutes les étapes de production.
Le processus de qualification selon cette norme est particulièrement exigeant, avec des audits approfondis des systèmes et des procédés. La démonstration de la maîtrise des processus spéciaux comme le traitement thermique ou les contrôles non destructifs est un point crucial. Les fournisseurs doivent également mettre en place des indicateurs de performance pour suivre en continu l'efficacité de leurs processus.
Traçabilité et documentation technique requise par l'ERA
L'Agence de l'Union européenne pour les chemins de fer (ERA) impose des exigences strictes en matière de traçabilité et de documentation technique pour les composants critiques comme les essieux. Chaque essieu doit être identifié de manière unique et l'ensemble de son historique de fabrication et de contrôle doit être archivé.
La gestion de cette
documentation doit être gérée de manière rigoureuse pour garantir son intégrité et sa disponibilité sur le long terme. Les systèmes de gestion électronique des documents (GED) permettent de centraliser et sécuriser l'ensemble des informations techniques. La mise en place de workflows de validation électronique assure la traçabilité des modifications et des approbations tout au long du cycle de vie des essieux.L'ERA impose également la conservation des enregistrements relatifs aux contrôles non destructifs, avec les images brutes des inspections ultrasonores ou magnétoscopiques. Le stockage sécurisé de ces données volumineuses sur le long terme constitue un véritable défi technique et organisationnel pour les fabricants. Des systèmes d'archivage à long terme, basés sur des technologies comme le cloud ou les supports optiques, sont mis en place pour garantir la pérennité des informations.
Challenges de la conception pour la fatigue et la durabilité
Modélisation par éléments finis des contraintes dynamiques
La modélisation par éléments finis est devenue un outil incontournable pour analyser le comportement des essieux sous sollicitations dynamiques complexes. Les simulations permettent de prendre en compte des phénomènes difficiles à appréhender expérimentalement, comme la propagation des ondes de choc lors d'impacts. La modélisation du comportement non-linéaire des matériaux et des interfaces, notamment au niveau des assemblages pressés, constitue un défi majeur pour obtenir des résultats représentatifs.
L'intégration des données issues du monitoring en service dans les modèles numériques ouvre de nouvelles perspectives. Les techniques de recalage de modèle permettent d'affiner les simulations en se basant sur les mesures réelles. Le concept de jumeau numérique, associant modèle physique et données d'exploitation, permet un suivi en temps réel de l'état de fatigue des essieux. Ces approches nécessitent cependant des capacités de calcul importantes et une gestion efficace des flux de données.
Optimisation topologique pour la réduction de masse
L'allègement des essieux est un enjeu majeur pour réduire la consommation énergétique des trains et l'impact sur l'infrastructure. Les techniques d'optimisation topologique permettent d'explorer des géométries innovantes, maximisant la résistance pour une masse donnée. La prise en compte des contraintes de fabrication, comme les rayons de raccordement minimaux pour le forgeage, complexifie cependant le processus d'optimisation. Comment concilier les formes organiques issues de l'optimisation avec les contraintes industrielles ?
L'utilisation de matériaux avancés comme les aciers bainitiques ou les alliages d'aluminium à haute résistance ouvre de nouvelles possibilités pour l'allègement. L'hybridation des matériaux, avec par exemple l'utilisation de fibres de carbone pour le renforcement local, est également explorée. Ces concepts innovants soulèvent cependant des défis en termes de tenue à long terme et de comportement en cas d'accident. Des campagnes d'essais approfondies sont nécessaires pour valider leur fiabilité sur l'ensemble du cycle de vie.
Tests de fatigue accélérés et validation des prototypes
La validation expérimentale des nouveaux concepts d'essieux reste une étape incontournable. Les essais de fatigue accélérés, réalisés sur des bancs spécialisés, permettent de simuler plusieurs années d'exploitation en quelques mois. La représentativité de ces essais vis-à-vis des conditions réelles d'utilisation constitue cependant un défi majeur. Comment reproduire fidèlement l'ensemble des sollicitations subies par un essieu au cours de sa vie, des chocs aux vibrations en passant par les effets thermiques ?
L'instrumentation avancée des essieux en test, avec l'utilisation de jauges de déformation à fibres optiques ou de techniques d'émission acoustique, permet un suivi précis de l'évolution des dommages. Les méthodes statistiques comme les plans d'expériences ou l'analyse de fiabilité sont largement utilisées pour optimiser les campagnes d'essais et extrapoler les résultats à l'ensemble de la population d'essieux. La validation des modèles prédictifs de durée de vie, intégrant l'ensemble des facteurs d'influence, reste un enjeu majeur pour garantir la fiabilité à long terme des essieux.